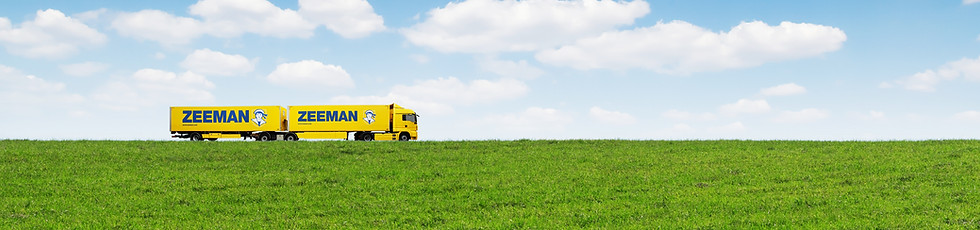
Zuinig of people.
Our suppliers.
​
Since May 2019, we are transparent about the locations of the factories that manufacture products for Zeeman. By signing the Transparency Pledge, we confirm our commitment to greater openness. Zeeman does not have its own factories, so the factories we use also produce for other brands and retailers. We invest in long-term partnerships and know the factories we work with well. All our factories have signed our Two-Way Code of Conduct.
​
In addition, 100% of our 1st tier suppliers and a part of our 2nd tier suppliers like spinning mills can be found on the website opensupplyhub.org, where any overlap with other brands and retailers is also visible. We report annually on the major points for improvement that emerge during factory inspections. By being open, we enable stakeholders to address potential points for improvement. In addition, this openness has given us more insight into the overlap that exists with other retailers in shared factories.
Since May 2019, we are transparent about the locations of the factories that manufacture products for Zeeman. By signing the Transparency Pledge, we confirm our commitment to greater openness. Zeeman does not have its own factories, so the factories we use also produce for other brands and retailers. We invest in long-term partnerships and know the factories we work with well. All our factories have signed our Two Way Code of Conduct. With 98% of our 50 biggest suppliers, we have been working for five years or longer.
​
​
​
​
​
​
​
​
​
​
​
​
​
​
​
​
​
​
​
​
​
​
​
​
​​100% of our first-tier suppliers and a part of our 2nd and third-tier suppliers like spinning mills can be found on the website Open Supply Hub, where any overlap with other brands and retailers is also visible. We report annually on the major points for improvement that emerge during factory inspections. By being open, we enable stakeholders to address potential points for improvement. In addition, this openness has given us more insight into the overlap that exists with other retailers in shared factories. 
You can also take a look at our supply chain on this world map. Here you can navigate to the different countries and see where the production sites are located. 100% of our tier-one suppliers are disclosed on this world map. We share the following details: name, address, number of employees, the start date of partnership, whether they make textiles or other products, and whether they use sustainable cotton and/or have Oeko-Tex certification. The data is updated annually.

Steering Committee Responsible
Business Conduct.
At Zeeman, we believe it is essential that corporate responsibility has an important place within all departments. We also want all colleagues to be involved in the CSR policy. In order to make everyone more aware of this, we went into depth about this subject during a number of brainstorming sessions. All departments set concrete goals to become more sustainable within their own profession. The Supervisory Board supervises the management's policy and the implementation of the strategy, and also monitors whether the interests of the various stakeholders have been adequately considered.
Two committees are active within the Supervisory Board: the Audit Committee and the Remuneration Committee. For board members, at least 25% of the bonus to be achieved is linked to people & planet business objectives. These are determined annually by the Remuneration Committee, which also determines the extent to which the objectives have ultimately been achieved.
The Zeeman family is 100% owner. That is why the family is always involved in important strategic choices.
Monitoring the supply chain.​
We want all our supply chain partners to comply with our Two Way Code of Conduct. Through our membership with Fair Wear, suppliers are audited on working conditions. Currently, 100% of all factories have been inspected by an independent party. Among other things, we check whether the working conditions are clean and safe and that there is no forced labor, discrimination, or child labor. In addition, we check the factory's quality procedures. Besides, we think it is very relevant to announce the date of an audit in advance to maintain a transparent relationship with the supplier. We do this at 100% of the audits that are taking place.
​
We also critically look at the impact of our own purchasing practices on the working conditions of suppliers. We recognize the impact they can have. That is why for example we pay all our suppliers 14 days after goods are shipped. Every year, Fair Wear reviews our efforts by measuring how well we have assessed, identified, and resolved issues in our supply chain. In August 2024, Zeeman earned a ‘good’ score of 68%. The score was the same as in 2023, but the percentage is a bit higher, up from 59% in 2023. In 2023, Fair Wear adjusted the assessment methodology to align with the OECD guidelines. The indicators make use of the due diligence action plan, so the methodology focuses more on our risk approach. This raises the bar for all the members.
In 2024, Fair Wear’s assessment indicated that we had made progress on the themes of discrimination and gender inequality. For instance, steps have been taken to better identify discrimination against women. It’s a long road, but more and more data is being collected. Data analysis could help identify issues more clearly. In 2025, we will continue along this path. We are also actively committed to launching new Living Wage programmes every year to reduce risks around wages.
Our aim is to do a little better every day. Read the detailed report here.

Two-Way Code of Conduct.
Zeeman has developed an extensive two-way code of conduct for all the parties we work with and for our own buyers: the Zeeman Two-Way Code of Conduct. 
Its main elements are: living wage, no forced labor, no discrimination, no child labor, and safe and hygienic working conditions. Our aim is to consolidate a supplier base that positively impacts the quality, transparency, and value of the product as well as lowers the risks of labor rights violations. However, sometimes ending business relationships is inevitable and necessary for these occasions we created a procedure with a responsible exit strategy. Also sometimes starting with new suppliers is needed.
When we start working with new manufacturers we follow the Zeeman new supplier procedure. The CSR team is involved in the decision-making and onboarding of new suppliers.
​
At Zeeman, we value long-term partnerships. We use our business relationships to achieve positive changes in factories with regard to working conditions. Our aim is to have strong leverage (on average 30-40%) at suppliers.
Living wage.
​
We want the employees of Zeeman’s manufacturers to earn a living wage. In other words, a wage that is sufficient to cover all basic needs, such as housing, transport, food, and healthcare. 5 new programmes have been developed in 2024based on the data obtained in 2023. They were launched on 1 January
2024. In total, we now have 10 Living Wage programmes where we finance a living wage at specific suppliers, representing 26% of the purchase value of clothing and textiles (Fair Wear’s scope) in Turkey, South Asia and East Asia.
​
Our approach.
Just like in the Netherlands, in our manufacturing countries the statutory minimum wage is set by the government. In countries such as India, Pakistan and Bangladesh, this minimum wage is not enough to cover a person's basic living costs. We believe all of our suppliers’ employees deserve a
living wage. Therefore, we help suppliers to finance a living wage for our share of the production.
Back in 2019, we started a programme with workwear manufacturer Schijvens at a joint factory in Pakistan. For our share of the production there, we now pay the difference between the minimum wage and the living wage. This project was still ongoing in 2024. Since 2022, programmes have been in place at a total of five suppliers. One is with an Indian supplier where we work closely with Prénatal: together, we account for more than 90% of the factory’s orders. Other programmes are running at suppliers in Bangladesh (two), Pakistan (one) and Turkey (one). Since 1 January 2024, we have been providing the Living Wage programme at five new suppliers: one in China, one in Pakistan, one in Bangladesh, one in Turkey and one in India. In the process, our approach to existing programmes has also been slightly modified. Initially, the amount paid out was adjusted for each payment based on goods recently shipped. But as a result, the monthly supplement fluctuated. We have since decided to fix the amount paid out for the whole year based on the previous year’s shipments. This allows us to give suppliers and workers the security of a stable living wage over a longer period of time, even if there are temporarily fewer orders. The programmes that started on 1 January 2024 are therefore based on 2023 data. We will start some new programmes in 2025.
​
​
​
Cooperation.
To make living wages possible, it is very important that the supplier is open to this and sees that the benefits outweigh any disadvantages. In addition, our partner Fair Wear is important. They guide us in making the calculations in the Fair Price app and with the introduction of living wages. We also learn a lot from members of Fair Wear who are already further along in this. They are an important source of best practices.
Goals.
We place nearly three-quarters of our purchase value with just fifty suppliers. Our share of production with these suppliers is therefore significant. This is an important point if we want to ensure that workers in the factory actually see their incomes increase when we enable living wages for our share of the factory’s production. To enhance this effect, we are also exploring whether there are other brands/retailers we can partner with. The intended result: higher wages. In determining the wage gap, we consider the difference between the lowest-paid wage and the living wage. Our goal for 2027: for at least 50% of our purchasing value, we make a living wage possible for our share in production.
​
Method.
​
We selected suppliers based on our turnover, production share, location, and relationship (which must be long-term). We then went through the calculation and the approach with the relevant suppliers and - if necessary - adjusted it.
​
We will evaluate the programs properly every year. For example, we want to draw up online questionnaires: employees can then indicate anonymously what the extra allowance means for them. In addition, we want to ask local NGOs such as Fair Wear to interview various employees. We hope to gain an even better understanding of the impact of the program this way. The next step is to present our approach to other retailers who are active in the factories. Because the more companies participate, the greater the impact.
​
​Within the living wage programs we always close the wage gap for our share of production. Therefore, the wage gap in Bangladesh is closed for approximately 25%. In Turkey for 56%. And for India 88%. And for Pakistan 48%. For every country the approach is slightly different due to, for example, tax costs. For the programs in Pakistan and India we work together with another Dutch retailer and together we are able to close the gap for almost 100%.
Country
Bangladesh
Turkey
India
Pakistan
Lowest paid wage
8000 BDT
5500 TL
9776 INR
25000 PKR
Target wage
16000 BDT
9470 TL
17775 INR
28500 PKR
Zeeman Project
Zeeman supported 1 supplier increased wage to 9680BDT + 1 supplier increased wage 10240BDT
Zeeman supported 1 supplier increased wage to 7723 TL (we also include tax costs additionally)
Zeeman supported 1 supplier increased wage to 16775 INR
Zeeman supported 1 supplier increased wage to 26680 PKR
Our buying practices.
​
Zeeman under the microscope.
​
Sustainable buying means that, besides quality and price, the effects on people and the environment are also taken into account during all aspects of buying. In order to increase the integration between CSR and buying, regular consultation takes place between the CSR & Quality, and Buying departments.
​
Suppliers are used to being assessed. On the safety of their factories, on their impact on the environment, and also on price, quality, and the timely shipping of our orders. We turned this around in the 360-degree evaluation. In 2020, we asked our factories to rate us on our buying practices using 56 questions. This could be done anonymously, so they had the freedom to give honest answers. 171 suppliers in the Far East and Turkey completed our questionnaire. We analyzed the valuable results of this study in 2021. These were then shared with the buying team. The following are some points to pay extra attention to during the buying process. These points are laid out in the Two Way Code of Conduct. Two Way because both the manufacturer’s and the buying party’s responsibilities are defined.
-
Suppliers sometimes accept orders whose delivery time is too short. This can have a negative impact on, for example, overtime and hiring of staff, and can therefore lead to higher production costs and poorer working conditions.
-
Zeeman places orders for basic textiles well in advance, by six months or sometimes as long as a year. Within these contracts, numbers shift regularly, which causes problems for some suppliers.
-
A quarter of suppliers reported that they accepted orders whose purchase price was lower than the cost. Our guiding principle is that all parties in the supply chain should benefit. But sometimes a supplier accepts lower prices because otherwise, they have too few orders or they don’t want orders to go to their competitors. Also, sometimes a supplier makes an error in the cost estimate, or material prices may have increased between accepting the order and buying the materials needed.
​
A responsible cost price
​
Our raison d’être is to sell products at the lowest possible price. We’ve been doing it for 55 years. But what exact price is possible is partly determined by our suppliers. That is why we are increasingly asking how the cost price is structured. We don’t want to negotiate a purchase price that is below the cost of production and that the factory can’t earn anything. Because that can have a negative impact on the working conditions of its workers.
​​​
Women in the garment and textile industry.
​
Zeeman is a long-time supporter of several projects in South Asia, on the principle of giving back
to our production countries. The goal of those projects is to prevent sexual exploitation of girls and
aid girls and young women who have become victims of human trafficking. In 2024 we launched a
new project in Pakistan with an entirely different focus: women’s participation in the workforce.
​
India.
We've had a presence in Mumbai in India since 2005. Our partner the Vipla Foundation runs a project for us there, called Save Our Sisters. The project helps girls who have been rescued from forced prostitution. The rescued girls are taken in by the local authorities, and we provide support to help them build a new life.
​
In 2024, our various programmed helped 698 girls. 208 of them received an education, from primary schooling to vocational training. 25 girls chose entrepreneurship training, while 93 opted for beauty & wellness and garment making. In total, we helped 6 girls find employment and guided 42 girls in establishing their own small businesses. The girls we help in this programme receive three years of follow-up support.
We also helped to organise numerous group sessions to provide psychological support for girls admitted to shelters after their rescue. Some 300 girls took part in those sessions. We also help to provide legal support to girls who manage to initiate criminal proceedings against the people responsible
for their human trafficking.
Zeeman’s focus for this project is determined every year. In 2025, we will continue with the 2024 programme. We will also set up a digital documentation system for compiling and accessing all the legal documents and other information.
​​​
Bangladesh.
In Bangladesh we have a project similar to the one in Mumbai, on the Indian border. Between 2016 and 2022, we supported other shelters in Bangladesh that housed girls rescued from prostitution. Because those organisations could not meet our standards, however, we had to find another organisation.
We now have an effective partnership with a new shelter.
Many of the young girls working in prostitution in India are from Bangladesh. The project's goal is to take in these girls as soon as they arrive at the Bangladeshi border after being rescued in India, and give them shelter and guidance. The new shelter was up and running by the second half of 2023, with capacity to take in 20 girls. Between March and December 2024, the project provided shelter for a total of 43 trafficking victims. Another 8 girls were saved from sexual exploitation before it could occur.
​
As part of the project, we see whether its possible to return the girls to their families. We help them process the trauma, provide them with education and follow up with them after they leave the shelter. We also do a lot of prevention work in the area around the shelter. In nearby villages, we provide counselling sessions for parents and young girls in the 10-16 age bracket. We warn them about the tactics that pimps use, to prevent girls from being drawn into prostitution. We also encourage them to go to school. We believe it’s important to support these preventive sessions such as these: the results can't be quantified, but the impact is often great.
​
Pakistan.
Where our focus India and Bangladesh is on helping young women recover from prostitution and human traficking, in Pakistan we focus on women’s participation in the labour market. The project draws funding from a subsidy from the Netherlands Enterprise Agency (RVO). In Pakistan, it is still common for women to be banned from working in factories. The project provides groups of women with training and
equipment so that they can work independently in Zeeman's partner factories. Previously, those factories almost exclusively employed men.
In 2024, we joined with Schijvens Corporate Fashion to launch a project at 3 factories, 2 of which are suppliers of Zeeman. At each factory, a group of 30 women have been selected to receive training so that they can work in a sewing workshop. The factories had to update their facilities, creating separate spaces for women. The male workers have also been prepared for the new situation. A visit to Pakistan in 2024 showed how well the project is going, and that the women are very proud of the path they have taken. Earning their own money suddenly gives them new opportunities and possibilities, allowing them to help pay for their children’s education or save money for a wedding.The project will be reviewed at the end of 2025. Although initiatives like this require a significant cultural shift, we hope to expand the project to other factories as well.​​​
Sustainable partnerships.
​
In order to achieve constructive improvements, cooperation with other retailers and companies, local NGOs and governments is important. That is why we are working together within a number of multi-stakeholder initiatives to improve working conditions.
Fair Wear Foundation.
​
In October 2019, we became a member of the Fair Wear Foundation. This means, among other things, that the people who make our clothing and textiles have a safe working environment, receive a living wage, and don’t work too much overtime. You can trust that we adhere to Fair Wear's Code of Labor Practices (CoLP) everywhere we do business. These rules are based on those of the International Labor Organization (ILO):


-
No forced labor
-
Freedom to join a union and bargain
-
No discrimination in the workplace
-
No child labor
-
Payment of a living wage
-
Reasonable working hours
-
A healthy and safe work environment
-
A legally binding employment contract
These labor practices are translated into the languages of the following countries: China, Bangladesh, and India. Fair Wear works with local experts. They inspect and supervise our factories on-site. In addition, a poster will be displayed in all our factories – in a visible place – informing employees of their rights. The poster includes a phone number for a helpline that employees can call if they feel the factory is not following the rules. Reports from factory employees go directly to Fair Wear, who will then contact Zeeman. And together, we'll look for a solution. This system is a solid, targeted complement to our own monitoring. It helps us further improve working conditions in our factories.
​
Every year, Fair Wear reviews our efforts by measuring how well we have assessed, identified, and resolved issues in our supply chain. In 2020 the Brand Performance Check was carried out for the first time since our membership. We have received the 'Good' rating, which means that we are well on the way. Of course, there are also areas for improvement, which help us determine the next steps. Our aim is to do a little better every day. Read the detailed report here.
​
Factory monitoring
In 2022, 19 audits took place executed by Fair Wear. Additional to this audit, FWF organized a Workplace Education Program (WEP) training to create awareness among the workers on all labor standards as described above. They provided training to both factory managers and workers inside the factory. The aim of this training is to support the social dialogue in the factory which leads to open communication regarding issues and opportunities to improve the working conditions. In 2022, 22 suppliers were trained by Fair Wear.
The poster including the helpline of Fair Wear can contribute to the potential improvements. Therefore, the WEP training is giving in-depth information on the purpose of the poster and the workers will be informed on how to use this complaint mechanism. 
 
Complaints mechanism
In 2022, seven complaints were reported through Fair Wear's complaints mechanism (helpline). Three were from Bangladesh, one from Turkey, one from Pakistan, one from China, and one from India. In the event of a complaint, we work together with the local Fair Wear team, other Fair Wear members, local NGOs, our agent, and the relevant supplier. We think it is positive that more complaints have been reported through the helpline. It shows that the mechanism has come to the attention of the employees. They feel confident enough to make a report. Find the complaints and remediation process here. Find an example of a complaint here. Find an English version of the Fair Wear helpline poster that is hung up in all factories here.
Systemic risks in the chain.
​
In the past year, we have developed a risk declaration form. A specific form has been created for each production country with a description of three social and environmental risks based on the severity and likelihood that a negative impact occurs. This risk prioritization is the result of our due diligence process for which we have made various risk analyses. A stakeholder meeting held in 2022 provided important insights for this, but also Fair Wear audits at suppliers, research reports from NGOs, and what we ourselves see in the chain.
In the risk declaration, our suppliers receive a number of questions for each prioritized risk. It is important to find out whether our suppliers are aware of the risk and how they deal with it. Next year we will evaluate the results and formulate an approach. We will also update this document if our annual risk analyses give reason to do so.
In addition, we base our approach on major risks that we see in the chain. Based on this risk prioritization, we can select projects and/or set objectives. A major risk in the production country Pakistan, for example, is the inequality between men and women. In addition, we see that freedom of association and social dialogue is often limited in a country like Bangladesh.
International Accord.
​
In August 2021, Zeeman signed the new International Accord for Health and Safety in the Textile and Garment Industry for a period of 26 months. This is a continuation of the previous Bangladesh Accord. The new agreement is meant to apply not only to Bangladesh but also to other countries. On January 24, 2023, we signed the new Pakistan Accord. We are convinced that the Pakistan Accord will contribute to further improvements in safety and working conditions in Pakistan in the coming years.
​
We continue to do our best to improve working conditions in the Bangladesh textile industry. The factories have done a lot to improve the points raised by the Bangladesh Accord safety inspections. Three kinds of inspection have taken place under the Accord at every manufacturer in the country: fire safety, building structure, and electricity. In addition, factory employees have been trained to report unsafe situations to supervisors. There is also a complaint mechanism, that enables factory workers to report safety-related complaints. At the factories where Zeeman is active, 97% of the original points for improvement had been implemented as of the end of 2021 (2020: 95%). The Accord average across all factories at the end of 2021 was 92%. In 2022 this was 94%,

IRBC Agreement on
Sustainable Garments
and Textiles.
​
In 2016, Zeeman signed the Dutch IRBC Agreement on Sustainable Garments and Textiles (AGT). The AGT ran until the 31st of December 2021. A broad coalition of businesses and other organizations worked together during the term of 5.5 years to improve working conditions, prevent pollution, and promote animal welfare in production countries. Within the AGT, participating companies have implemented the OECD Guidelines, with regard to doing Human Right Due Diligence. Over the past 5 years, companies supporting the Agreement received advice, tools, and training to help them create and implement their policies. The aim was to identify the risks within the supply chain to people, animals, and the environment, and to tackle abuses. In this final year of the Agreement, Zeeman held a score of 82%. This met the minimum of 80%. At this time, substantive work is underway on a possible continuation of the Agreement into the Next Generation Agreement (NGA). When the new Agreement will take effect is not known at this time.
​
​
​
Goodweave program
​
In the Panipat region of northern India, we have been participating in a Goodweave program in recent years to gain a full picture of the supply chain of Indian suppliers. The NGO Goodweave is committed to completely eliminating child and forced labor in the industry. Where this does occur, the program provides education within the community where the child lives.
​
The suppliers of four of our direct suppliers have been made transparent and assessed. Each supplier within this project uses a large number of sub-suppliers. Every active supplier has been inspected by Goodweave. Any points of attention have been passed on to us. An example of this is the lack of a child labor policy. The risk of child labor was not found. The program was rounded off in 2022. We are currently looking for a follow-up to this program.

Supply Chain Project Turkey & Unicef
Together with other signatories of the textile agreement and UNICEF, we are working on a project aimed at improving children’s rights in and around textile factories in Turkey. This has already proven to be a success in Bangladesh. In 2021, a local party was also connected for the implementation work: Fair Labor Association (FLA). This project is based on the Children’s Rights and Business Principles (CRBP). A set of 10 voluntary principles developed by UNICEF, the UN Global Compact and Save the Children. The CRBP framework guides companies on the full range of actions they can take in order to respect and support children’s rights - the working environment (within the walls of the factory), the community (around the production location), and the marketplace (where the product is sold). The CRBP guidelines offer a starting point for the analysis and development of responsible business practices, where children’s rights are respected and the well-being of families and children is improved.
​
In joint meetings with UNICEF and FLA, the entire chain was mapped from the two suppliers directly affiliated with this project. In addition, both UNICEF and FLA visited our two suppliers and their subcontractors. In a joint meeting with our team, UNICEF, FLA, and suppliers the findings of the visits were presented, including an analysis of the supply chain and risks for child labor. One of the recommendations was to introduce codes of conduct and/or contracts between our direct suppliers and their own suppliers. Based on this, we helped them set up a code of conduct. The next steps include for example improvement of working conditions for working mothers. Such as a childcare service at the factory and a place to breastfeed or to breast pump.
​
Read the project two-pager here.
​​​
COVID-19 policy.
​
Our agents and suppliers are our partners. For this reason, we have decided to adopt a targeted approach with the goal of continuity for both our partners and Zeeman itself. Partners with whom, in many cases, we have been doing business for decades. The three most important issues in our Covid-19 policy for suppliers are:
-
We will not extend our payment term, always 14 days without exception, in this crisis. We are maintaining this as usual and have reconfirmed it to our suppliers.
-
We have contacted all our suppliers individually regarding current orders: spring orders have largely been shipped already as agreed, some orders have been deferred by mutual agreement, and a small portion has been stored and will be shipped next year. The bulk of our range consists of basic textile products. Long-term contracts have been signed for these. Within the terms of these contracts, we shift numbers according to demand, with the guarantee that 100% of the products will be accepted.
-
We are also demonstrating our commitment to suppliers for future orders.
We continuously monitor what the consequences of the Covid-19 crisis are for each supplier, not only in terms of financial continuity but also, in particular, in terms of employee welfare. In doing so, we align ourselves with the statement issued by Fair Wear, which also assigns a major role to brands when it comes to wages for garment workers.
To reinforce our approach, Zeeman endorses the ‘Call to action’ as drawn up by the ILO in collaboration with various international parties active in the clothing sector.​
​